システム開発・製品化
Products
2020/02/04
開発・導入事例
これまでに手掛けてきたお客様の抱える様々な技術的課題の解決をお手伝いさせて頂いた例を以下に紹介させて頂きます。
例1)
A社:工場生産ラインの溶剤塗布検査
目的:検査の自動化によるコスト削減と生産効率の向上
概要
製品加工に必要な溶剤塗布工程の後で、灰色の溶剤が完全に塗布されているか否かを自社製の色抜けセンサにて識別。その情報を高速で製品搬送する回転体を通じて上位CPUへ非接触で電力及び塗布結果の識別情報を伝送。画像処理と違い、カメラや画像処理エンジン、適切な照明等を必要とせず、リーズナブルなシステム。また、非接触ゆえメンテナンスフリーであり、導入頂いたお客様には今もずっとご愛用頂いていております。
システムの構成と特徴
電磁誘導の原理を応用し、比較的近距離の空間を隔てて信号と電力の非接触伝送が可能
稼働機構の運動側から固定側にスイッチやセンサの情報を伝送すると共に固定側から運動側に電力を伝送
従来のスリップリング、FMテレメータ、ケーブル交換方式に置き換わるFA化の効率的手段
特長
- 空間ギャップ最大50mmの非接触伝送
- 運動側に電源や電池が不要、外来ノイズに強い
- 情報伝達が迅速でチェックが完全
- 水・油・埃等の悪環境でも使用可能
- 小型、軽量で耐震・対加速度性に優れる
動作原理(図解)
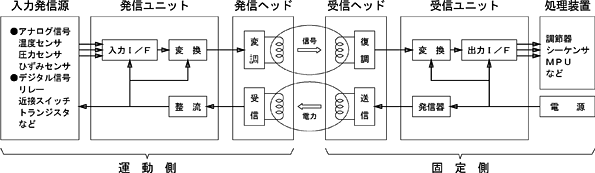
導入効果
- 消耗部品が無いので、ランニングコストは「ゼロ」!
- 機械メンテナンス時に、分解組立が非常に簡単。
- 防滴防塵対応により、食品加工ラインのオンライン洗浄に対応。
スリップリングとカプラの比較
メンテ性 | イニシャル コスト | ランニング コスト | 特徴 | |
スリップリング | × | ○ | × | ・都度ライン停止しての交換作業必須 ・年間にしてイニシャルコストの4~6倍 |
カプラ | ◎ | △ | ◎ | ・ライン停止する必要なし! ・電気代のみ! ・初期投資は必要 |
例2)
B社:製品の外観検査システム
目的:検査の自動化及び各種センサでデータ収集し、歩留率改善
概要
製品の組立工程にて、ワークが規格通りの加工がなされ、製造されてきたかどうかを各種センサよりデータ収集し、その結果を上位サーバーへデータ転送するシステム。
現場の搬送ライン側より製品種類や番号等の情報を貰い、各種情報へ紐付け。それらに市販の画像処理装置や変位計にて測定した情報を集計し、予め設定した閾値に対する合否判定や、画像や変位データの全てを上位へ転送し、その後の生産工程の歩留率改善に用いられている。
検査対象に対しS/N比が良くなるよう適切な照明を用意。
システムの構成と特徴
単なる平面ではなく、3次元でのデータを採取。製造ライン上での末端にあたる部分でデータを採取し、上位サーバーへEthernet経由にてデータ送信するまでを担当する。
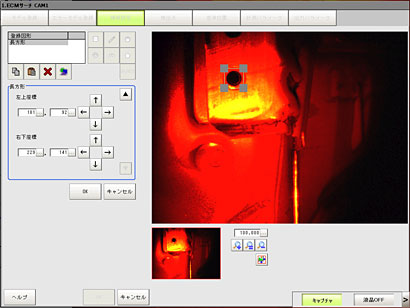
導入効果
歩留率が飛躍的に改善!
閾値を適宜設定することにて、従来の手法ではずっと後ろの工程にて不良品と判定されていた不具合を早期発見することが可能になり、その結果歩留率を飛躍的に改善することに成功した。